Although powder metallurgy is used in many different applications, most parts typically fall into one of the four categories shown below, each of which has its own unique design considerations:
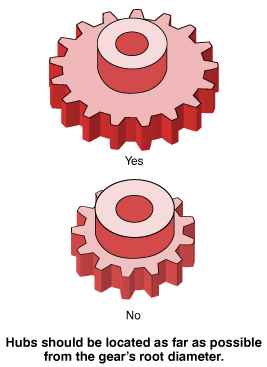
Gears
Gears are well suited to PM production:
- Carbide dies provide long life and accuracy.
- Residual part porosity tends to dampen sound.
- PM gears can be made with blind corners, thus eliminating the need for undercut relief.
- PM gears can be combined with other configurations such as cams, ratchets, other gears, and various components.
- Helical gears are possible; copper infiltration sometimes used to improve teeth densities.
- Since tooth shape is not a problem, true involute gear forms are easier to produce through PM than through other fabrication methods.
Here are some things to keep in mind when designing PM gears:
- Note that the center hole location relative to the gear shape is affected by the running tolerances of the various tool members. This makes it more difficult to hold close TIRs obtainable with arbor-cut gears, and hubs or pinions that increase the number of concentric tool members increase TIR tolerance needed. TIRs can be reduced by grinding gear IDs true to the gear pitch diameter.
- As the AGMA Class of gear increases, so does the cost of the gear because of the secondary operations required to meet the tighter tolerances.
- To avoid having very thin tool members, gear hubs or pinions should be located as far as possible from gear root diameters (see figure).
Cams
Cams are well suited to PM production:
- The process provides excellent surface finish and part-to-part consistency.
- The natural finish of a self lubricating PM cam will often outwear a ground cam surface.
- For radial cams, the cam shape is formed in the die; for face cams, the shape is formed in the punch faces.
Assemblies
- Two or more PM parts can often be joined to form a unit that is difficult, if not impossible to make as a single structure.
- Capitalizing on PM’s flexibility, it is feasible to make assemblies of very different materials: a bronze bearing in a ferrous structural part, for example, or a heat-treated part with a non-heat-treated part.
- PM parts can be joined by conventional methods such as staking, press fitting, brazing, soldering, welding, epoxying, riveting, bolting, and also by sintering together materials of appropriately different size change characteristics.
- Copper infiltration during sintering can be used to bond steel parts.
Bearings
- Bearings are a natural product for PM because of its controlled porosity and the resulting self-contained lubrication.
- Plain bearings, flanged bearings, spherical bearings, and thrust washers are commonly produced.
- The operating environment should be carefully considered: external lubrication, cooling, and hardened or chromium-plated shafts tend to increase permissible loads. Repeated start-stop operation, oscillatory or reciprocating motion, high speeds, shock loads, and temperature extremes tend to decrease permissible loads.
- For detailed information on permissible loads, press-fits, and tolerances, see the engineering section in MPIF Standard 35, Material Standards for PM Self-Lubricating Bearings.