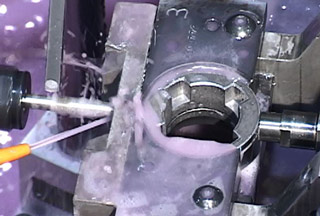
A sintered powder metallurgy (PM) component can be finished or treated just like any other metal component to achieve desired characteristics—corrosion resistance, improved strength and hardness, surface wear resistance, edge-sharpness relief, porosity sealing, and control of size and surface finish.
Plating, coating, deburring, welding, furnace brazing, heat treating, and steam treating are among the secondary operations that are used successfully in the process of fabricating finished PM parts.
Unlike components made using other metal forming processes, powder metallurgy components can be repressed or coined, as well as sized, to densify or modify the surface shape and provide stricter dimensional control. Through oil impregnation, used on PM self-lubricating bearing components since the late 1920s, components can absorb 12%–30% oil by volume. Resin impregnation can also be performed on PM components to improve machinability or to prepare the surface for plating. Infiltration is a secondary process step used to either improve strength or seal parts and make them gas- or liquid-tight. Optionally, like resin impregnation, it can also be used to enhance machinability, improve ductility and prepare parts for plating.
Read a whitepaper on machining powder metallurgy parts for even more detail.
The following tables detail how various secondary operations are applied to PM components.